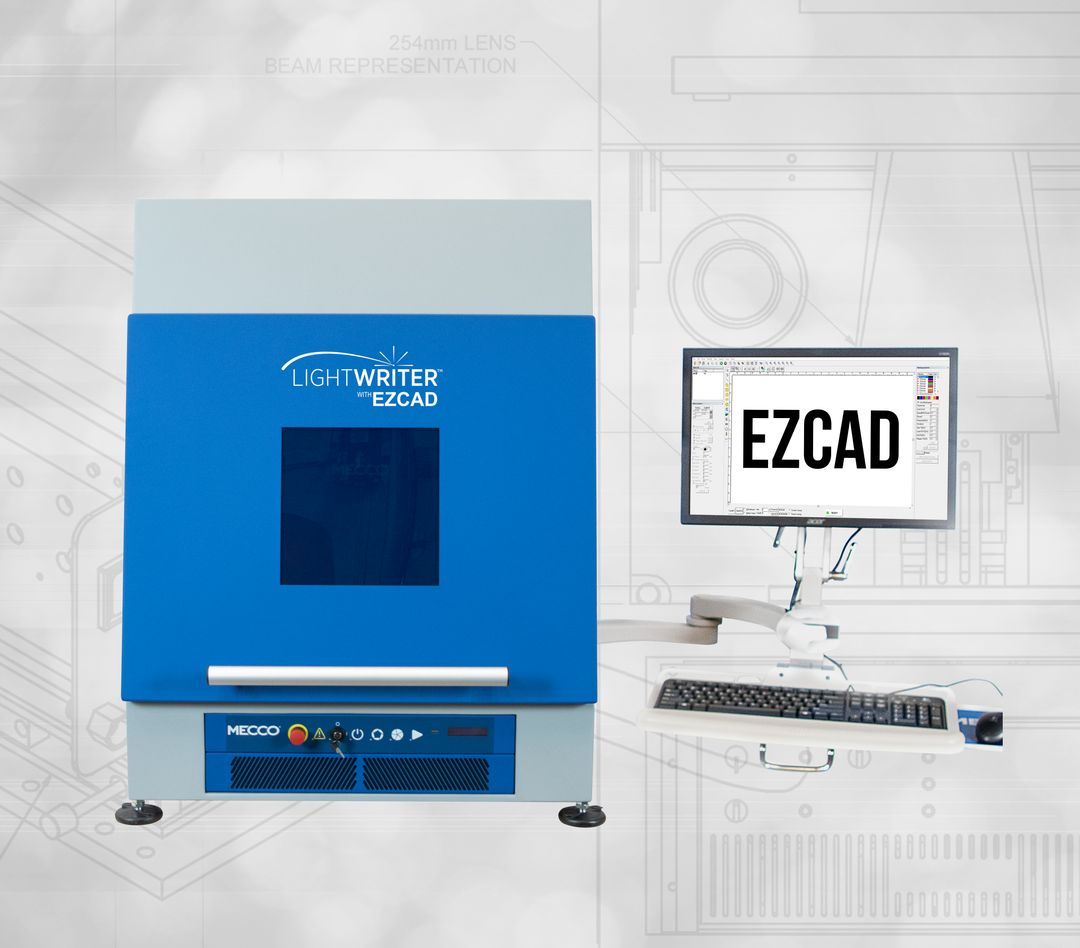
EZCAD Familiarity MECCO Quality
MECCO now offers customers our quality-built LightWriter Class IV, 600 and 800 series with EZCAD, enabling you to upgrade your fiber laser marking systems while reusing your existing job files without the need to retrain your staff; saving you time and money.
MECCO’s LightWriter Class IV, 600 and 800 series with EZCAD offer a best-in-class, complete, easy, economical, all-in-one benchtop fiber laser marking solution for an array of applications.
Be ready for any challenge with the compact versatility of LightWriter™.
Why MECCO
EZCAD Convenience
The LightWriter Class IV, 600 and 800 series with EZCAD allow you to retain existing customer job files built with white-label software (MiniLase Pro). Preserve essential parameters (laser power, speed, frequency, and focus settings) to ensure precise and efficient marking of materials.
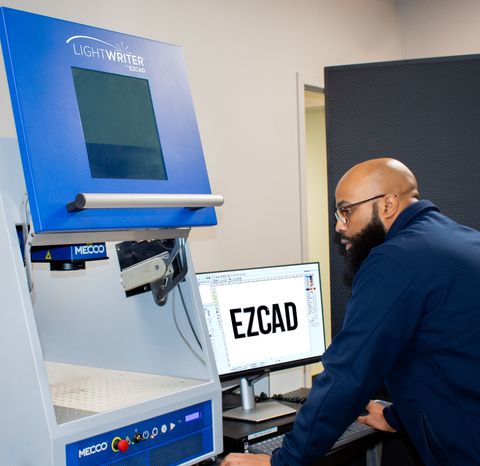
Parts & Service
MECCO stocks compatible components (lasers, scan heads) that allow us to service existing laser engraving systems as well as other EZCAD-based providers.
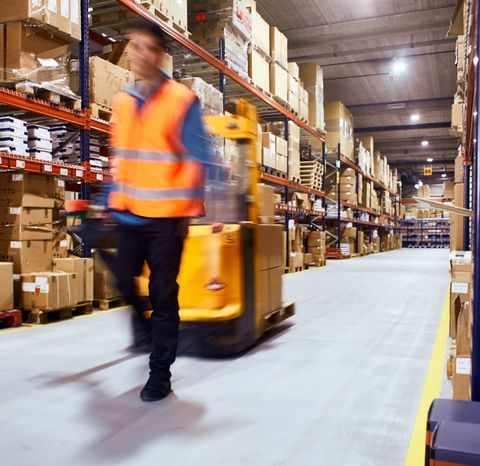
Industry-Best Technical Support
MECCO leads the industry in solution turnaround time, parts inventory and replacement, technical support, and customer satisfaction.
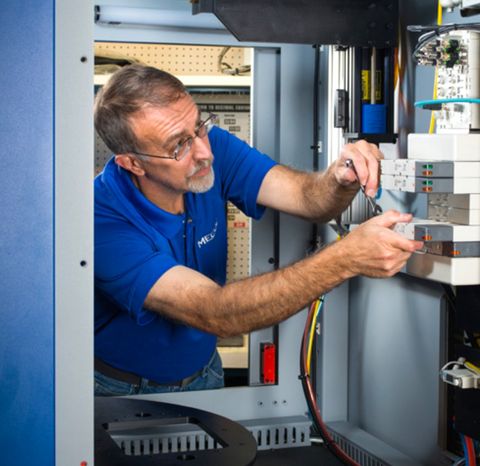
Less Downtime
MECCO uses the highest-quality components and designed the LightWriter Class IV, 600 and 800 series with EZCAD to keep your benchtop fiber laser marking systems running to meet production goals, reduce downtime, and prioritize employee safety.
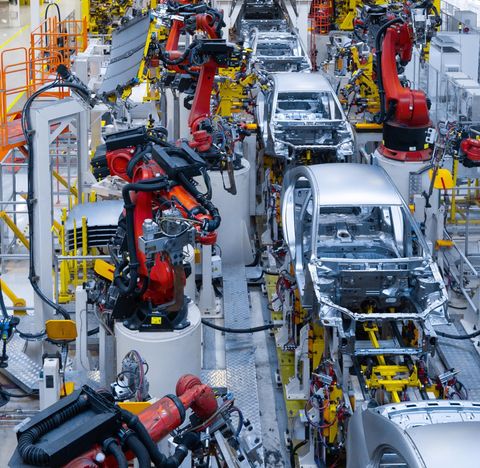
Customers We Have Served
MECCO quality delivers reliability and less downtime
Industrial Hardware
MECCO's pride in our products means high-quality components capable of standing up to extreme conditions thanks to our durable steel enclosures designed to withstand 100lb. max part weight and daily use.
Software and Network Connectivity
MECCO quality means smooth operation without the worry of software corruption or connectivity interruptions.
Optical Alignment
MECCO sourcing and design delivers repeatable alignment of the laser optics, ensuring the efficiency of the laser marking process.
Setup and Operation
Our deep bench of technicians save you time and money by ensuring proper setup and operation – and you can reuse your job files, and avoid retraining staff.
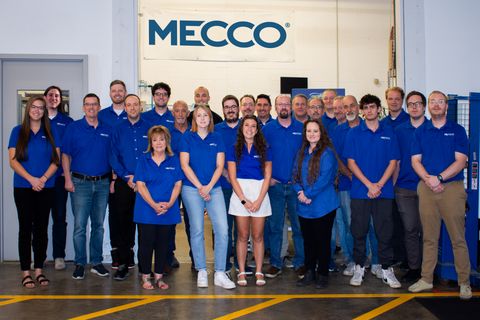
MECCO is Here to Stay
135
Years of Innovation
24
Hours
Same-Day Responsiveness
#1
2016 Manufacturer of the Year
A+
Superior Technical Support
Welcome to the MECCO Experience
We connect every customer with a team of MECCO application, integration, and service experts to ensure production quality, throughput, time-to-market, and uptime.